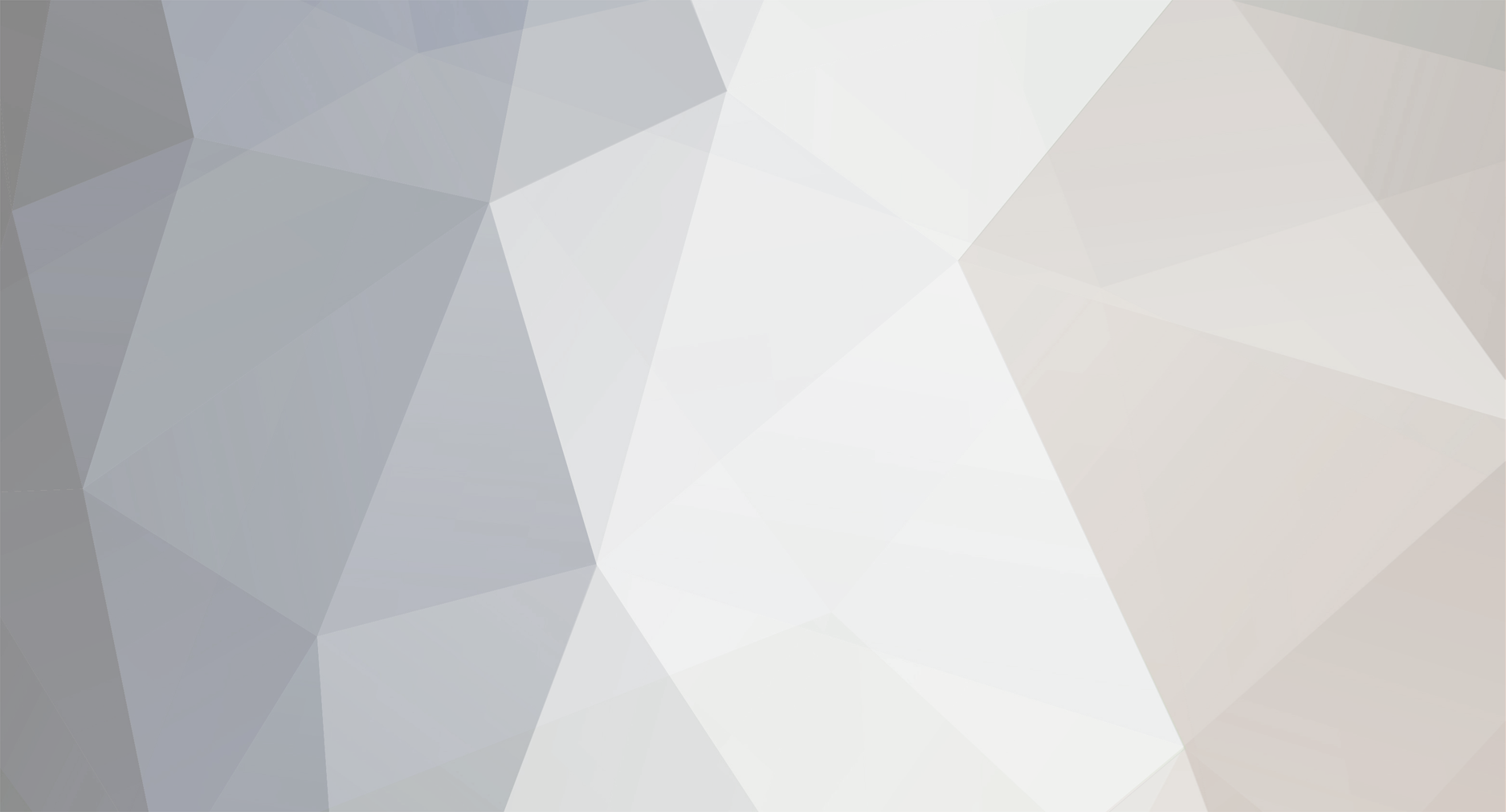
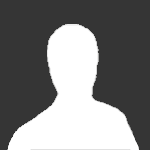
Mikexx
Member-
Posts
580 -
Joined
-
Last visited
Profile Information
-
Gender
Male
Recent Profile Visitors
4,016 profile views
Mikexx's Achievements
Proficient (7/12)
31
Reputation
-
Like IanD I am very sceptical. Solar panels are dark to the eye so highly absorptive of sunlight. The efficiency for flexible solar panels is a nominal 15% For rigid panels probably 20%. The rest of the solar power falling onto the panel will be converted directly to heat that will escape by a combination of thermal radiation, air cooling and conduction to a roof. Having a layer of insulation below a flexible panel seems the worst of all worlds.
-
I have difficulty believing that claim. The actual temperature seen by an IR thermometer is very dependent on emissivity and the wavelength of the sensor. Same goes for paint where the attained temperature in sunlight is also very dependent on colour. We ought to be painting our roofs white to keep things cool! A contact thermocouple might give more consistent measurements.
-
If the corrosion was external, then this would have had nothing to do with battery DC polarity but down to other causes, such as shore line earth bonding or lack of appropriate anodes.
-
As an electrical engineer I understand that anything positive wrt to an electrolyte is bad news where the metal will simply be eaten away through oxidisation corrosion. But given the limited areas that a wire electrode can enter an electrolyte such as water it is rare that there would be any internal galvanic corrosion on a boat. In the explanation by Gibbo the most likely time this could occur would be a frayed wire, and certainly no one would be any the wiser. I do therefore agree with you that a negative earth is the ideal but it's a marginal advantage. On cars there are many external connections and surfaces that are open to the elements hence the preference of a negative earth. The irony is that a coil with a positive earth is deemed more efficient to generate a spark with the hot electrode being negative.
-
Mikexx started following The weather , Starter motor BMC Captain 1500 , Solar Panel mounts and 3 others
-
I'm going to bite. While it is ideal for the hull to be negative wrt to the surrounding water (hence why we have anodes), what difference will being a negative earth be over a positive earth? Or are we talking internal corrosion within the boat itself?
-
Wish I was aware of them a few years ago when I fitted the panels. You still need a hole for the cable of course but the roof will look less like a pepper pot!
-
I used the mounts in the link I provided earlier. A centre bracket is bolted to the roof. The outside rail is free to fall on the roof and in my opinions is unsatisfactory as it will damage the roof paintwork, hence why I added the feet at each corner. I do like the magnetic idea, perhaps using something like these: https://www.amazon.co.uk/CDIYTOOL-Neodymium-Magnets-Threaded-Non-Slip/dp/B0BY19LWJR
-
I added feet that gave some clearance and protected the top paintwork: https://www.amazon.co.uk/Uni-Fine-Adjustable-Stainless-Regulating-Furniture/dp/B085T36SG2 I think I was able to miss my mushrooms.
-
That's why I got these tilting solar mounts: https://midsummerenergy.co.uk/buy/solar-panel-mounting/Narrowboat-Tilt-Mount There aren't many inches clearance under the M5.
-
I wouldn't sand anything that would make the steel thinner. Best knock back into position as per other posts. I recall having a vehicle that used elongated spreader washers including some corner ones to reduce sump distortion. You can get generic oval washers although their size will be critical to fit between the lips on the sump. An example: https://www.groveco.co.uk/contents/en-uk/p1475.html eBay also have loads and the sellers may be more compliant in providing measure dimensions. Moss also sell them for MG timings covers However after looking at your photo of your sump, given the indents I would go for the largest plane washer that would fit in the space.
-
I never said it was when it came to homes. I feel you have taken my quote entirely out of context. In fact the sentence was about a motorhome responding to a post by the OP that I even quoted in my reply.
-
HMRC are very clear about what is Zero Rate VAT. To my knowledge it is zero rated only if it is adapted for disabled use. Therefore I am surprised about your claim or it was a while ago. I suppose there is nothing to stop you having the vehicle modified, say with a chair lift as long as it conforms to HMRC criteria. However the application form VAT1615A requires (note even HMRC can't spell): The disabled person named in this declaration usually uses a wheelchair for their mobility and the permanently and substantially adapted vehicle is for their personal use. And The disabled wheelchair user named in this declaration is chronicaly sick or has a disabling condition (provide brief details below) and the adaption of the vehicle is necessary because of this condition Quite, as per definition of avoidance. I'm sure those using the old K2 schemes would like you to think they are not 'avoiding paying' tax too.
-
My understanding is that 'avoidance' is a term for legally not paying a tax using recognised tax rules. Some avoidance schemes may be a sham but new self-build houses are certainly a genuine way of avoiding paying VAT, or should I say being able to claim the VAT back. Tax evasion is just that, not paying taxes that are due by illicit means, normally not declaring the income. A butty that is without an engine towed to a mooring would fulfil the rules of a houseboat. That could then be sold by the maker with 0% VAT. The new owner wouldn't normally be VAT registered and so anything they do would not be subject to a VAT inclusive price if they sold it on. So, if the rear of the boat had some swim plates[1] and an engine added at a later date, while those costs would be subject to VAT the original VAT claimed by the boat builder wouldn't be charged to the new boat owner. Not sure if that would still make economic sense unless you were adding a classic engine to the 'house-boat'. [1] I added this as the boat must not be readily adaptable to accept a form of propulsion so perhaps shouldn't have swim plates. I guess depends on how many butties have swim-plates.
-
And the journey continues, but doesnt look as expensive as I thought
Mikexx replied to Mike on Sea Hustler's topic in BMC
Is there anything stopping you carrying red and green filters in your pocket as visual aids when coming across coloured lights? After all if they allow glasses to correct sight then .................... -
Did you forgot to mention the man with a red flag in front of lorries? 🙂